Mark Hewitt Pottery. Firing 98 and Kiln Opening. December 2017.
Here are a few snaps from the firing...
Early on. Still only a little fire in there: stoking hardwood logs.
Terry Childress (local potter and sculptor extraodinaire) stoking the main firebox.
Mark salting the front of the kiln with the help of Malcolm Henry.
The orange red glow of the pots at the end of the firing.
Here's one of Stillman's that we pulled out still hot!
The 98th Salt Kiln Firing Crew.
The main day of the firing was a blustery fall day but the heat of the kiln kept us comfortable. I am particularly happy with some of the egg vases that I made; I've tried small versions of this shape before but never larger ones. My pitchers and barrel mugs are gradually getting better -- eking toward the goal of Mark's light, elegant forms.
In other news, the bee hives down in the apple orchard are doing well: they have survived the winter thus far. Fingers crossed! We might even get some honey next year. The garden is producing, too -- I picked some nice broccoli for dinner tonight and there are more than enough cabbages to have a sauerkraut party.
On to the pots!
First up, here's the big pots from this cycle, in the dusty grey morning light.
Mark Hewitt. Big pot. $4,500.
Mark Hewitt. Big pot. $3,500.
Close up of the decoration. I like the lilac circles on this one.
Mark Hewitt. Big pot. $4500.
Mark Hewitt. Big pot. $4,500.
Mark Hewitt. Big pot. $6,500.
Mark Hewitt. Big pot. $6,500.
Mark Hewitt. Big pot. $6,500
Mark Hewitt. Big pot. $7,500.
Close up of the decoration. I helped dot this one... so many dots!
Standing proud.
Now lets get into the sale, and smaller pots.
Mark giving his morning address before the punters get their pick of the pots. First come, first served!
The orderly walk down to the barn.
The Fervour.
The Fervour Part II.
A local artist painted a picture of Mark which graced the wall of the barn this weekend.
Various pots by Mark.
Cookie jar and pitcher. Mark Hewitt.
Top row = black slipped pots with cadmium yellow rims. Bottom row = ash glazed pots. All made by Mark.
Nice ash glazed ten gallon pot surrounded by bowls.
Mark's blurb from this opening.
Some more of Mark's ten gallon pieces.
Fancy wig stand by Mr Hewitt.
Close up of the decoration.
Now on to some flatware...
Mark Hewitt. Bowls with fern decoration.
Mark Hewitt. Pie dish. Ash glaze with blue glass drips.
These plates had a red slip liner which Mark decorated through and then glazed over with a glaze made from a local gravel.
Mark Hewitt. Bowl.
Mark Hewitt. Plate.
Mark Hewitt. Plate.
Mark Hewitt. Platter.
Mark Hewitt. Platter.
On to the planters...
Waves of planters!
Some of my planters in the foreground, Mark's in the back.
Mark Hewitt. 120lb planter.
Mark Hewitt. Monster planter.
Mark Hewitt. Rouletted salt glaze planter with blue glass.
One of my planters, simple wavy incised lines whilst it was on the wheel.
Some of Stillman's and my pots.
Lots of little shooters, plus Stilly's bud vases and bio.
Stillman's blurb from this firing.
Shoppers grazing.
Its nice to see customers who come with their own boxes.
The pots always look better in the sun.
One of my spoon holders that got buried in wood ashes.
Two of Stillman's bud vases and one of my canister jars.
One of my mixing bowls.
Mixing bowls, all lined up.
Mixture of mine and Stillman's pots.
More apprentice pots!
My shelf -- with blurb in the background.
Some more shelves of mine and Stilly's pots.
Two of my tumblers on the shelves.
And now, in case you have not seen enough pottery, here's a few more of mine with the barn as a backdrop.
Hamish Jackson, 1 1/2lb pitcher and 2 1/4lb pitcher.
Hamish Jackson, 3/4lb creamers.
Hamish Jackson, Water (or beer) bottle.
Hamish Jackson, Egg Vase. I like the ashy side of this one: nice dramatic firing.
Hamish Jackson, Pebble Vase.
Hamish Jackson, Egg Vase.
Hamish Jackson, Salty Mugs.
Hamish Jackson, 3 1/2lb casserole dish.
Hamish Jackson, Beer Tankard.
Hamish Jackson, Bud Vase.
To end here is a great moment I captured of a customer photographing his pots in front of the compost heap.
The heap is getting its time in the limelight!
I had to take the picture he got, too -- too good to miss. The worm bin I made is in the back right, too. Got to give the worms a shout out.
Finally, here's a picture of some of the kiln shelves that once again need grinding. The myth of Sisyphus springs to mind!
This is not all of the shelves by the way.
Becoming a Beekeeper: My first year keeping bees in North Carolina.
I've been interested in beekeeping for some time, but never had the impetus to start until I became friends with some local beekeepers when we moved to Chatham County. I joined the Chatham County Bee Association and started going to their 'Field Days' at the Community College in Pittsboro. The association manages an apiary there for teaching purposes. I had never seen a hive worked before and it immediately made me want to get into it. Seeing the frames of bees and honey being removed from the hive and inspected was magic. Going to association's monthly meetings showed me that there was a whole world to learn about bees and beekeeping.
Local beekeepers told me to take "Bee School," a bi-annual class run nearby in Pittsboro, before getting my own hives. I was absolutely going to take this advice, but an opportunity presented itself in the fall when a chap in the association wanted to get rid of his hives. He had started them the previous spring and they were doing well, but his niece and nephew had been stung a few times. So I took the opportunity and got them.
I'll describe my first year beekeeping by the season, as it is a highly seasonal pursuit.
AUTUMN
I got the hives on September 11th 2016. They had been started off from packages in the spring of 2016. They had grown up to fill out two deep boxes and one medium each.
My master/mentor Mark and his wife Carol kindly let me put the hives on their property, down in in the apple orchard behind the pottery. I weed-whacked around the area and put down a tarp to help prevent weeds taking over and set up breeze blocks on flat spots for the hives. I wanted to expand the apiary to four hives, so I leveled and set up those spots in advance. It's nice having the hives at work as I can go and check on them at lunchtime.
A couple of friends who are beekeepers helped me move them and advised me on preparing for overwintering. In our area, it's common to have to feed the bees diluted honey water or sugar water in Autumn to make sure they have the food stores to get through winter. I didn't have to feed them much, though, as they had decent enough stores already. Moving them wasn't too bad--we did it at night, with a wire mesh stapled to the front entrance of the hives to stop any bees escaping. We tied a ratchet strap tightly around each and used a hive lifter (which clamps under the handles) to get them onto the bed of the pick up truck. The journey was only about five miles, but I was still worried all the way there!
We arrived safely and placed them down carefully, leaving the hive closed for a couple of days. Once opened up, the bees reoriented themselves by flying in circles around the hive. It was pretty cool to see, but I made sure to give them some space and not disturb them for a couple of weeks, just observing from a distance.
I named the hive on the left Rosemary and the one on the right Thyme. Bees actually hate thyme oil so this was a poor choice in retrospect. I din not know this at the time. Rosemary has always been a step ahead of Thyme.
My first major mistake was being convinced that Rosemary did not have a Queen. I could not see any sign if her, nor eggs or larvae. So I found another Queen and introduced her to the hive. I introduced her slowly as you are supposed to... putting her in a cage watched inside the hive for 3 days. When 3 days were up I let her out, only to see her balled up by workers. They stung her till she was no more. It was a sad moment. The workers are very sensitive to a new Queen with different pheromones, and will only accept her if they really are Queenless. The Queen slows down laying at the end of Autumn and stops altogether in winter so this is what must have occurred: I didn't see any fresh eggs because she wasn't laying.
In early October 2016, we had a scare from Hurricane Matthew, so I prepared the hives as shown below. Thankfully the main part of the storm missed us, and the hives were fine.
WINTER
Once the weather got cold, I pretty much left the hives alone. You don't want to open them up and let warmth out during the winter. On the occasional warm day, I had a peek in to see how the stores were holding up. It was a pretty mild winter by all accounts, apart from a couple of brutal weeks, and they came through fine, with no additional feeding. Come January/February, I gave them a little pollen and sugar to get them excited for spring.
"Bee School" ran in the winter--one evening every week from eight weeks--and taught me a lot about bees. In particular, I learnt about bee biology and how their colony functions. Bees are complicated creatures! It was an excellent course and I thoroughly recommend taking a similar course if it is available in your area--but there is a big difference between the theory of beekeeping and the actuality of working a hive.
One of the best parts of bee school was the equipment building week.
Going out to the field days and watching inspections in action taught me more of the physical and practical skills. It's ideal to find a mentor to show you the ropes if possible; I've been fortunate enough to have several people to discuss problems with and to come and help out.
SPRING
Once the weather warmed up some (Febuary/March), the bees started going out and foraging again, and the Queens started laying eggs again.
Both of my hives built up pretty fast--in part I think because of the pollen I gave them (not sure I will do this again). By the time I did a full inspection with a beekeeping friend, the hives had already both swarmed.
I was slow on the uptake and totally missed the signs (Queen cells) and a cramped hive. So in early Spring I had two hives with zero Queens. Bad news. But I did have four Queen cells in one hive, and five in the other. These are larger cells which the workers feed extra Royal Jelly (bee superfood) and then the egg develops into a Queen. If you have more than one emerge at the same time, they will fight to the death! If one emerges before the others then she will go and sting all the other Queen cells before they can. There can only be one Queen in any house!
With the help of Gerald Wert--an experienced local beekeeper--we split these two hives into five, each with one or two Queen cells. I would have never taken such a dramatic course of action, but now see it was the right course of action. I only wanted four hives, but Gerald advised to make more just in case. The hope was that each of them would make a new Queen, but sadly two of them didn't take. This is not uncommon. So I combined two of the hives (one Queenless with one Queen right) and managed to procure a VSH Queen (see below) from a local supplier to put into one of them. So at the end of spring, I had four laying Queens in four hives. They were weak but Spring is the time of year when there is plenty of forage out there for the bees.
Marjoram and Basil had joined the apiary!
SUMMER
Early summer is typically when beekeepers extract honey in my area. I was all excited and ready to try in June, managed to borrow a centrifugal extractor, and had all my equipment set and ready. Unfortunately, upon full inspection it was clear that the hives didn't have enough stores for extraction. I was not hoping to take much, the hives being young and all, but it was still a tad disappointing. I could have taken a few frames from Rosemary, who was the heaviest by far, but the Queen had been up in the honey supers, laying eggs on the back of frames of honey... this meant that if I extracted that honey then those babies would be lost. I wasn't about to do that! There was literally only one viable frame, which I took and scraped out. It was enough to fill one small glass jar. It tastes good though: we've been enjoying it for breakfast (sparingly) on sourdough toast.
I did a "sugar shake" to see how many varroa mites were in each hive. Varroa mites are the worst pest affecting bees worldwide (except possibly humans). They only made their way to North Carolina in 1990 but have been wreaking havoc since. Last year, 40% of all bee hives were lost in our state, and this is at least in part due to varroa mites. They spread viruses and diseases and can weaken the colony significantly.
There are guidelines for how many mites is acceptable in a hive, laid out by the state inspectors and general literature. Nine mites per 300 bees is the maximum that is acceptable. Rosemary came in at three, Thyme at 18, Basil at 10, and Marjoram at zero. There are two main ways of dealing with the mites: treating the hive, as you would if you got head lice--with a chemical that kills them--or re-queening the hive. I decided to use Api-Guard, which is a product, somewhat ironically, made from thyme. It is a soft-chemical, but a chemical nonetheless, and I felt bad about inflicting it on the bees. It is not easy trying to kill a small bug on a larger bug. Next time I think I will try re-queening with VSH Queens... these are Queens who have been bred to be "hygienic:" their offspring tend to clean themselves super well, and dump the varroa mites off them.
The treatment worked well enough--I had a significant drop in varroa mites in those hives, and the Queens got back to laying again.
AUTUMN 2017
It was just about a year ago that I got Rosemary and Thyme. I have made many mistakes not to be repeated, and am currently just giving the hives a little sugar water to make sure they have enough food to get through the winter!
FURTHER MISTAKES:
It took me awhile to get over the sense of fear when pulling apart the home of 30,000 bees (I haven't counted, but that's a conservative estimate). To begin with, I got stung quite a bit: partly this was because I was clumsy... dropping a whole frame of bees usually means you are going to get stung! Also, going down to the apiary without a lit smoker is silly--even if you try not to use it, its nice to have if the bees get riled at all. It blocks their pheromones and tends to make them more docile.
Going barefoot is a bad idea when inspecting, and shorts can also be problematic. Trousers with elastic bands around your ankles are really nice so the bees don't crawl up your legs. I don't practice this, but can see how it would be nice! A veil is essential when you are starting out--the bees tend to fly at your face and eyes when defending the hive. Having not tied my veil up properly and been stung on the eyebrow once, I know the value of the veil. Gloves tend to hinder me more than help, though.
One time I got stung quite a few times in one place on the thigh (wearing shorts), and came out in hives all over my body. Had to nip down to emergency care for a shot of steroids in the buttocks. Apparently this can happen if you get stung right in a vein. I have only had this reaction once. Fingers crossed it doesn't happen again. I now have an EPI pen in my beekeeping stuff too.
OTHER BASIC INFO:
Life cycle of the honey bee:
Worker bee service:
1-2 days: Cleaning cells and warming the brood nest, eat pollen and beg for nectar by older bees passing by.
3-5 days: Some of earlier tasks plus feeding older larvae with honey and pollen.
5-8 days: Nurse bees-hypoparyngeal gland is well developed so they can produce royal jelly to feed young larvae and Queen bee.
8-12 days: Take/process incoming food; ripen honey/store pollen.
12-16 days: Wax glands well developed; produces wax and constructs comb, ripens honey.
17-21 days: Guards hive entrance and ventilates hive, orientation flights.
22 days +: Forage for nectar, pollen, propolis and water.
Helpful Resources:
The CCBA (Chatham County Bee Association) has been amazing; I would have struggled much more had it not been for them. Each meeting has a different speaker come and present on a specific topic such as "using honey as medicine" or "tackling varroa mites." Whilst some of this goes over my head, I always learn things.Wherever you are, join the club--beekeepers who will more than likely want to help you with your bees.
In North Carolina, we have an amazing resource at our disposal--the state-supported (and funded) Apiary Services Program. NC is divided into six zones, each with its own inspector. You can call them out to check on your bees. Ours is Don Hopkins: he is extremely knowledgeable, and taught the bee school section on diseases, pests, and pest management.
There are a lot of books on beekeeping out there, but these are a few I have enjoyed and found useful:
First Lessons in Beekeeping by Keith S. Delaplane
Beekeeping for Dummies by Howland Blackiston
The Beekeeping Bible by Richard A. Jones and Sharon Sweeney-Lynch
I recently took a test to be basic "Certified" beekeeper but it goes up to Journeyman, Master and Master Craftsman. Heres the site: www.ncbeekeepers.org/master-beekeeper-program
Some beauty to end on:
Honey and bees! |
Local beekeepers told me to take "Bee School," a bi-annual class run nearby in Pittsboro, before getting my own hives. I was absolutely going to take this advice, but an opportunity presented itself in the fall when a chap in the association wanted to get rid of his hives. He had started them the previous spring and they were doing well, but his niece and nephew had been stung a few times. So I took the opportunity and got them.
I'll describe my first year beekeeping by the season, as it is a highly seasonal pursuit.
AUTUMN
I got the hives on September 11th 2016. They had been started off from packages in the spring of 2016. They had grown up to fill out two deep boxes and one medium each.
My master/mentor Mark and his wife Carol kindly let me put the hives on their property, down in in the apple orchard behind the pottery. I weed-whacked around the area and put down a tarp to help prevent weeds taking over and set up breeze blocks on flat spots for the hives. I wanted to expand the apiary to four hives, so I leveled and set up those spots in advance. It's nice having the hives at work as I can go and check on them at lunchtime.
A couple of friends who are beekeepers helped me move them and advised me on preparing for overwintering. In our area, it's common to have to feed the bees diluted honey water or sugar water in Autumn to make sure they have the food stores to get through winter. I didn't have to feed them much, though, as they had decent enough stores already. Moving them wasn't too bad--we did it at night, with a wire mesh stapled to the front entrance of the hives to stop any bees escaping. We tied a ratchet strap tightly around each and used a hive lifter (which clamps under the handles) to get them onto the bed of the pick up truck. The journey was only about five miles, but I was still worried all the way there!
The hives in their new spot.
|
We arrived safely and placed them down carefully, leaving the hive closed for a couple of days. Once opened up, the bees reoriented themselves by flying in circles around the hive. It was pretty cool to see, but I made sure to give them some space and not disturb them for a couple of weeks, just observing from a distance.
I named the hive on the left Rosemary and the one on the right Thyme. Bees actually hate thyme oil so this was a poor choice in retrospect. I din not know this at the time. Rosemary has always been a step ahead of Thyme.
Rosemary, in the back of the photo, building up like crazy--lots of foraging and new bees, whereas Thyme in the front is not doing so well. |
My first major mistake was being convinced that Rosemary did not have a Queen. I could not see any sign if her, nor eggs or larvae. So I found another Queen and introduced her to the hive. I introduced her slowly as you are supposed to... putting her in a cage watched inside the hive for 3 days. When 3 days were up I let her out, only to see her balled up by workers. They stung her till she was no more. It was a sad moment. The workers are very sensitive to a new Queen with different pheromones, and will only accept her if they really are Queenless. The Queen slows down laying at the end of Autumn and stops altogether in winter so this is what must have occurred: I didn't see any fresh eggs because she wasn't laying.
Experienced beekeeper Lori Hawkins on the right describing how to pick up a frame properly. |
In early October 2016, we had a scare from Hurricane Matthew, so I prepared the hives as shown below. Thankfully the main part of the storm missed us, and the hives were fine.
Hurricane prep. |
Once the weather got cold, I pretty much left the hives alone. You don't want to open them up and let warmth out during the winter. On the occasional warm day, I had a peek in to see how the stores were holding up. It was a pretty mild winter by all accounts, apart from a couple of brutal weeks, and they came through fine, with no additional feeding. Come January/February, I gave them a little pollen and sugar to get them excited for spring.
Me and some of my ladies. |
Bee School secrets inside. |
This is an empty frame, waiting for the wax foundation to be inserted into it. This thin layer helps get the bees started building comb. They will do it on their own but it helps speed things up. |
This is David Jones, demonstrating his homemade device for embedding the wax foundation onto the wire supports by sending a quick blast of electricity through them which melts the wax just enough. |
My hive tool resting on the box. The scraping side is helpful to remove sticky propolis, which the bees use to glue the hive together. The hooked side helps lift frames out of the box. |
SPRING
Once the weather warmed up some (Febuary/March), the bees started going out and foraging again, and the Queens started laying eggs again.
You can see some tiny tiny freshly laid eggs in this picture--they look kind of like rice. Unfortunately the Queen laid them in between the boxes in "burr comb" which broke as I opened the hive up. |
Spot the DRONE. There is only one here. |
I was slow on the uptake and totally missed the signs (Queen cells) and a cramped hive. So in early Spring I had two hives with zero Queens. Bad news. But I did have four Queen cells in one hive, and five in the other. These are larger cells which the workers feed extra Royal Jelly (bee superfood) and then the egg develops into a Queen. If you have more than one emerge at the same time, they will fight to the death! If one emerges before the others then she will go and sting all the other Queen cells before they can. There can only be one Queen in any house!
You can see worker larvae developing in these cells. The bee with its head in there is a nurse bee feeding the young larvae. |
With the help of Gerald Wert--an experienced local beekeeper--we split these two hives into five, each with one or two Queen cells. I would have never taken such a dramatic course of action, but now see it was the right course of action. I only wanted four hives, but Gerald advised to make more just in case. The hope was that each of them would make a new Queen, but sadly two of them didn't take. This is not uncommon. So I combined two of the hives (one Queenless with one Queen right) and managed to procure a VSH Queen (see below) from a local supplier to put into one of them. So at the end of spring, I had four laying Queens in four hives. They were weak but Spring is the time of year when there is plenty of forage out there for the bees.
Marjoram and Basil had joined the apiary!
SUMMER
Early summer is typically when beekeepers extract honey in my area. I was all excited and ready to try in June, managed to borrow a centrifugal extractor, and had all my equipment set and ready. Unfortunately, upon full inspection it was clear that the hives didn't have enough stores for extraction. I was not hoping to take much, the hives being young and all, but it was still a tad disappointing. I could have taken a few frames from Rosemary, who was the heaviest by far, but the Queen had been up in the honey supers, laying eggs on the back of frames of honey... this meant that if I extracted that honey then those babies would be lost. I wasn't about to do that! There was literally only one viable frame, which I took and scraped out. It was enough to fill one small glass jar. It tastes good though: we've been enjoying it for breakfast (sparingly) on sourdough toast.
A frame from one of Lori's hives: it is full of capped honey and ready for extraction! |
I did a "sugar shake" to see how many varroa mites were in each hive. Varroa mites are the worst pest affecting bees worldwide (except possibly humans). They only made their way to North Carolina in 1990 but have been wreaking havoc since. Last year, 40% of all bee hives were lost in our state, and this is at least in part due to varroa mites. They spread viruses and diseases and can weaken the colony significantly.
One frame removed. |
There are guidelines for how many mites is acceptable in a hive, laid out by the state inspectors and general literature. Nine mites per 300 bees is the maximum that is acceptable. Rosemary came in at three, Thyme at 18, Basil at 10, and Marjoram at zero. There are two main ways of dealing with the mites: treating the hive, as you would if you got head lice--with a chemical that kills them--or re-queening the hive. I decided to use Api-Guard, which is a product, somewhat ironically, made from thyme. It is a soft-chemical, but a chemical nonetheless, and I felt bad about inflicting it on the bees. It is not easy trying to kill a small bug on a larger bug. Next time I think I will try re-queening with VSH Queens... these are Queens who have been bred to be "hygienic:" their offspring tend to clean themselves super well, and dump the varroa mites off them.
The treatment worked well enough--I had a significant drop in varroa mites in those hives, and the Queens got back to laying again.
AUTUMN 2017
It was just about a year ago that I got Rosemary and Thyme. I have made many mistakes not to be repeated, and am currently just giving the hives a little sugar water to make sure they have enough food to get through the winter!
Some extra equipment I managed to get at a good price through the CCBA, ready for next year. |
FURTHER MISTAKES:
It took me awhile to get over the sense of fear when pulling apart the home of 30,000 bees (I haven't counted, but that's a conservative estimate). To begin with, I got stung quite a bit: partly this was because I was clumsy... dropping a whole frame of bees usually means you are going to get stung! Also, going down to the apiary without a lit smoker is silly--even if you try not to use it, its nice to have if the bees get riled at all. It blocks their pheromones and tends to make them more docile.
Going barefoot is a bad idea when inspecting, and shorts can also be problematic. Trousers with elastic bands around your ankles are really nice so the bees don't crawl up your legs. I don't practice this, but can see how it would be nice! A veil is essential when you are starting out--the bees tend to fly at your face and eyes when defending the hive. Having not tied my veil up properly and been stung on the eyebrow once, I know the value of the veil. Gloves tend to hinder me more than help, though.
One time I got stung quite a few times in one place on the thigh (wearing shorts), and came out in hives all over my body. Had to nip down to emergency care for a shot of steroids in the buttocks. Apparently this can happen if you get stung right in a vein. I have only had this reaction once. Fingers crossed it doesn't happen again. I now have an EPI pen in my beekeeping stuff too.
OTHER BASIC INFO:
Life cycle of the honey bee:
Type
|
Egg
|
Larva
|
Cell capped
|
Pupa
|
Average Developmental Period
|
Start of Fertility
| ||||||||
Queen
|
3 days
|
5 1/2 days
|
7 1/2 days
|
8 days
|
16 days
|
Approx. 23 days
| ||||||||
Worker
|
3 days
|
6 days
|
9 days
|
12 days
|
21 days (Range: 18-22days)
|
N/A
| ||||||||
Drone
|
3 days
|
6 1/2 days
|
10 days
|
14 1/2 days
|
24 days
|
Approx. 38 days
|
Worker bee service:
1-2 days: Cleaning cells and warming the brood nest, eat pollen and beg for nectar by older bees passing by.
3-5 days: Some of earlier tasks plus feeding older larvae with honey and pollen.
5-8 days: Nurse bees-hypoparyngeal gland is well developed so they can produce royal jelly to feed young larvae and Queen bee.
8-12 days: Take/process incoming food; ripen honey/store pollen.
12-16 days: Wax glands well developed; produces wax and constructs comb, ripens honey.
17-21 days: Guards hive entrance and ventilates hive, orientation flights.
22 days +: Forage for nectar, pollen, propolis and water.
Helpful Resources:
The CCBA (Chatham County Bee Association) has been amazing; I would have struggled much more had it not been for them. Each meeting has a different speaker come and present on a specific topic such as "using honey as medicine" or "tackling varroa mites." Whilst some of this goes over my head, I always learn things.Wherever you are, join the club--beekeepers who will more than likely want to help you with your bees.
In North Carolina, we have an amazing resource at our disposal--the state-supported (and funded) Apiary Services Program. NC is divided into six zones, each with its own inspector. You can call them out to check on your bees. Ours is Don Hopkins: he is extremely knowledgeable, and taught the bee school section on diseases, pests, and pest management.
There are a lot of books on beekeeping out there, but these are a few I have enjoyed and found useful:
First Lessons in Beekeeping by Keith S. Delaplane
Beekeeping for Dummies by Howland Blackiston
The Beekeeping Bible by Richard A. Jones and Sharon Sweeney-Lynch
I recently took a test to be basic "Certified" beekeeper but it goes up to Journeyman, Master and Master Craftsman. Heres the site: www.ncbeekeepers.org/master-beekeeper-program
Some beauty to end on:
Here's a picture of some native bees on a cacti flower, atop a cliff, on the island of St John in the Virgin Islands last Spring. |
Summer Kiln Opening, Firing 97, Mark Hewitt Pottery.
We were fortunate to have a mild summer's day for the firing; it was hot, but not obscenely so, and the kiln went up just fine. We weren't so lucky for the unloading, however. The air was so thick and sticky it felt like I was swimming in tar pit. I think we each lost about 5lbs in water that day. It takes us a whole week to load the kiln and just a single day to unload.
View into the firebox, early on in the firing.
It's always a day of mixed emotions; excitement mingling with disappointment, sweat mingling with blood (from nicks on sharp wads or ceiling stalagtites), and fine pots mingling with wasters. It is heavy work, moving all the kiln shelves and furniture out, as well as all the pots. We were all exhausted at the end of the day, but relieved with the results. Upon first glance it seemed like a good firing, and once we delved deeper, we found that it was an excellent firing all told.
Matt Hallyburton side stoking the kiln.
Flames out of one of the stoke holes.
The firing crew. Top row: Stillman Browning-Howe, Me, Joe Sink. Below: Luke Wheeler, Mark Hewitt, Matt Hallyburton.
It's been an enjoyable summer cycle of making at the Hewitt Pottery, with a little extra time than usual to make pots and experiment with new forms. The International Wood-Fire Conference (that Mark helped organise) took place in Seagrove and provided a chance to see a wide range of wood-fired pottery, listen to talks about all manner of ceramics-related topics, and draw inspiration from the wider community.
The "Great Pots" show at the Pottery Center was particularly useful; with over 150 pots from the traditions of North and South Carolina. To get to examine some of those old pots up close—particularly the surfaces of Solomon Loy and Chester Webster's incised decorations—was a real treat. A previous post of mine showed some of these pots with descriptions etc. The wood-fire conference as a whole was inspiring, and it prompted me to try various new forms such as rundlets, egg vases, and boxes.
Two of my rundlets (for whisky) and a squared off vase with heron incised decoration.
Is that a heron in a top hat? Yes. Yes it is.
Without further ado, I'll reel out the pictures of the kiln opening. The first weekend of the sale took place last weekend; the second is this coming weekend. The hours are 9-5 Saturday 2nd September and noon-5 Sunday 3rd September.
Mark addressing the morning crowd.
People prepared with baskets!
The procession down to the barn.
Customers scrambling to get the pots they liked best.
The seconds table. Always a bargain to be found here!
Mark's big pots.
Big pot. Mark Hewitt.
Big pot. Mark Hewitt.
Big pot. Mark Hewitt.
Big planter. Mark Hewitt.
Big pot. Mark Hewitt.
Customers in the inner barn.
Classic Mark Hewitt decoration: manganese slip lines and white slip dots.
Ash glazed wares by Mark Hewitt
Ten Gallon vase by Mark Hewitt.
Display of some of Mark's celadon work.
More pots by Mr. Hewitt.
Cutomers contemplating the ten gallon pieces.
A few rare yellow glazed pots.
Hot peppers on a salty platter.
Some wall vases by Mark Hewitt.
Vase by Mark Hewitt from right in the front stack of the kiln.
Drippy black slip!
Classic cookie jar of Mark's.
Ten gallon jar by Mark Hewitt.
Celadon plates by Mark Hewitt.
Dotty decorations. Flatware by Mark Hewitt.
Two of Mark's side plates.
More plates by Mark Hewitt.
Mark's platters hanging on the side of the workshop. These came out particularly well, so I have included a picture of each below.
Platter 1. Mark Hewitt.
Platter 2. Mark Hewitt.
Platter 3. Mark Hewitt.
Platter 4. Mark Hewitt.
Now some apprentice pots...
Fishy bud vase of Stillman's.
One of my 3/4lb honey jars.
Flowers in one of Stilly's bud vases.
Planters arranged for sale. Morning sun casting long shadows.
Nice bit of ash on this one of mine.
Loopdy loops.
Some of my mixing bowls.
One of my quart pitchers.
Mixture of shooters made by Stillman and I.
Mostly Stilly shooters.
Full shelves ready for the sale!
Stillman posing with one of his cute little bud vases.
One of my egg vases, sgrafitto decoration.
One of my handled bottles.
One of my sunflower quart pitchers. I was decorating these at the height of the sunflower bloom.
Another egg vase. Love the salty finish on this one.
Creme Brûlée dishes made by Stillman. He makes a damnably fine creme brûlée too.
A couple of my small footed bowls.
Some of my side plates (first batch) and wasabi dishes.
Custard cups made by Stillman.
One of Stilly's custard cups with loopdy-loop decoration.
More apprentice pots.
One of my two-part vases.
Trio of my celadon mugs.
A group of cups intimidating a poor little honey jar.
Two of my bottles behind one of Stillman's.
One of my little boxes, with blue glass on top.
Pots pots pots.
One of my heron mugs, inscribed: "Hey Baby, Nice Legs."
One of Stillman's egg vases to end on.
Wood-Fired Ceramics Exhibition, "Connected By Fire" at the Blue Spiral Gallery in Asheville, NC. June 2017.
Last month saw a great many wood-fire potters congregating in North Carolina. The International Woodfire Conference took place at STARworks NC, from June 8th-11th, with a week of pre-conference activities beforehand. I was lucky enough to be able to scoot up to the mountains of western NC to see the exhibitions going on and meet lots of great potters.
I spent a good bit of Saturday at Josh Copus' compound where two kilns were being busily loaded and anther being built. Josh curated Connected By Fire at the Blue Spiral Gallery in Asheville around a core group of artists who in turn invited others into the fold. I didn't manage to make it to the opening, but I got the place to myself on Sunday morning and had time and space to photograph the work. I did miss a cabinet of cups which was secreted away on another floor of the gallery, and a few of my pics were inexplicably blurry and had to be left out, but I saw most of it.
I thought it was a delightful display of wood-fired ceramics. The variety of surfaces is astounding; from the warm, glazed surfaces of Bandana Pottery's work, to the dramatic flashing achieved by Copus and Knoche, to the subtler, somber tones of David Peters' work, to the dark, stormy ash build up on Ben Richardson's Deflection pieces. There were surprises, too, such as Jeff Shapiro's ice flow piece which reminded me of an icing accident on a basalt cake, or Will Dickert's angular platters which had me imagining how many different types of nuts I could lay my hands on (seriously nice nut display opportunities), or Mr Oh's bizarre, whimsical wood fired sculptures.
The firings of the pieces in the show is crucial to their success. Speaking with Josh Copus, he said that he is thinking about the placement of every pot as he's making it in the studio, and not only this but that different local clays end up in different areas of the kiln based on how they look at different temperatures and levels of oxidation or reduction. You can see the care and consideration that was taken in the way these pieces were placed in the kiln and fired.
Many of the potters use local materials and their work exhibits a raw sensibility: a sense of the earth and the rocks and the geological processes that made them. Being a potter myself, these things greatly appeal to me. To know that slip came from the stream at the end of the potter's garden makes the piece so much richer. Seeing this work and talking with many of the artists involved was inspiring. To know that you can experiment with just about any material you find, and figure out whether it could be useful in a slip, glaze, or clay body, or even just as wadding to place pots on in the kiln, is very exciting.
It has opened my eyes to a different way of looking at clay. In my daily studio practice, we take clay, made now by Takuro Shibata at his clay factory at Starworks; pug it, weigh it out, and throw functional pots with it. The clay has to be plastic and fine in order to stretch it thin and throw large bellies into mugs or jars. But much of the work in this exhibition veers dramatically away from this way of working; Akira Satake's boxes and sculptures are so far from thinly thrown mugs. It almost seems like he hasn't worked the clay at all: the finished pieces feel so raw and natural, like mountains and trees.
Well, that's probably enough gesticulating from me. Enjoy the pictures!
Akira Satake, Sculptural Box No. 1. Wood-fired porcelaneous clay. 7.25 x 7 x 6.5. $625.
Eric Knoche, Untitled Line. Wood-fired stoneware with slips. 21 x 19 x 6. $3,500.
Akira Satake, Sculpture No. 2. Wood-fired porcelaneous clay. 17.5 x 10.5 x 7. $4,500.
Eric Knoche, Abacus No. 3. Wood-fired stoneware with slips. 28 x 45 x 3. $2,700.
Akira Satake, Kohiki Vase No. 3 (left) & Kohiki Vase No. 1 (right). Wood-fired stretched slip stoneware. $685 & $625.
Eric Knoche, Horseshoe Cloud. Wood-fired ceramics. 18 x 14 x 5. $2,000.
Eric Knoche, Chain. Wood-fired stoneware with slip. 77 x 8 x 7. $3,000.
Eric Knoche, Miscellaneous Symbols and Tools. Wood-fired stoneware with slips. 30 x 50 x 7. $3,300.
Close-up of: Eric Knoche, Miscellaneous Symbols and Tools. Wood-fired stoneware with slips. 30 x 50 x 7. $3,300.
Close up of: Eric Knoche, Miscellaneous Symbols and Tools. Wood-fired stoneware with slips. 30 x 50 x 7. $3,300.
Judith Duff, Wave. Wood-fired ceramics. 9.5 x 13 x 6. $650.
Judith Duff, Shigaraki Clay Bottle. Wood-fired ceramics. 15.75 x 5.75 x 5.25. $600.
Judith Duff, Ikebana Form. Wood-fired ceramics. 5 x 17 x 3. $450.
Catherine White, Echo. Wood-fired stoneware with natural ash glaze. 17.5 x 11 x 11. $900.
Catherine White, Spokes. Wood-fired stoneware with natural ash glaze. 6.5 x 13 x 12.5. $400.
Catherine White, Striation (left) & Kite II (right). Wood-fired stoneware with natural ash glaze. $200 & $500.
Catherine White, Pulse. Wood-fired stoneware with natural ash glaze. 10 x 9 x 6.5. $400.
Eric Knoche, Abacus. Wood fired-stoneware with slip. 30 x 50 x 7. $2,700.
Tim Rowan, Box. Wood-fired native clay. 8 x 7 x 6. $800.
Tim Rowan, Vessel. Wood-fired native clay. 23 x 9 x 10. $3,000.
Eric Knoche, Puzzle No. 2. Wood-fired stoneware with slips. 9 x 24 x 5. $2,300.
Hyang Jong Oh, Three Birds (sold as set). Wood-fired ceramics with slip and glaze. 36 x 9 x 6. $2,000.
Hyang Jong Oh, Musician Pagoda. Wood-fired ceramics. 27 x 12 x 12. $1,800.
Ben Richardson, Cleave No. 1 & 2. Wood-fired ceramics. 8.5 x 6. $600 each.
Left: Josh Copus, Large Stone Vessel No. 5. Wood-fired wild clay. 29 x 14 x 9. $900.
Right: Josh Copus, Medium Stone Vessel No. 9. Wood-fired wild clay. 20 x 9 x 9. $450.
Josh Copus, Large Stone Vessel No. 12. Wood-fired wild clay. 26 x 17 x 17. $900.
Josh Copus, Large Stone Vessel No. 4. Wood-fired wild clay. 30 x 17 x 12. $900.
Josh Copus, Small Pixels (sold individually). Wood-fired wild clay. 46 x 34. $30.
Left: Shozo Michikawa. Natural Ash Twist Form No. 2. Wood-fired ceramics. 8 x 4.5 x 4.5. $2,000.
Middle: Shozo Michikawa. Natural Ash Vase. Wood-fired ceramics. 11 x 3.5 x 3.5. $2,000.
Right: Shozo Michikawa. Natural Ash Twist Form No. 1. Wood-fired ceramics. 7.25 x 4.5 x 4.5. $1,800.
Shozo Michikawa. Tanka Bowl. Wood-fired ceramics. 5.5 x 13 x 12. $2,500.
Shozo Michikawa. Natural Ash Pineapple Vase No. 2. Wood-fired ceramics. 6.5 x 6 x 6. $2,000.
Ben Richardson, Deflection No. 1 & 2. Wood-fired ceramics. 12 x 5 x 3. $500 each.
Ben Richardson, Deflection No. 2. Wood-fired ceramics. 12 x 5 x 3. $500.
Josh Copus, Large Stone Vessel No. 2 & No. 11. Wood-fired wild clay. 25 x 15 x 6 & 28 x 17 x 16. $900 each.
Josh Copus, Orb. Wood-fired ceramics. 7 x 8 x 8. $250.
Josh Copus, Large Orb Vessel. Wood-fired wild clay. 19 x 16 x 16. $900.
Ben Richardson, As Darkness Falls No. 1 & 2. Wood-fired ceramics. 6 x 5.5 & 7 x 5.5. $600 each.
Josh Copus, Erosion. Wood-fired wild clay. 7 x 7 x 2. $240 each.
Will Dickert, Jar Study, No. 1. Wood-fired stoneware. 9 x 7 x 7. $200.
Will Dickert, Trough Form. Wood-fired stoneware. 8 x 9 x 28. $995.
Jeff Shapiro pieces. Details below.
Jeff Shapiro, Ice Flow Series No. 1. Wood-fired ceramics with natural ash deposit and glaze. 6.5 x 12 x 10. $1,600.
Jeff Shapiro, Untitled No. 1. Wood-fired ceramics with natural ash deposit and glaze. 21 x 9 x 4. $2,300.
Jeff Shapiro, Untitled No. 2. Wood-fired ceramics with glaze, ash, and shell marks. 15 x 17 x 4. $1,500.
Josh Copus, Large Stone Vessel No. 9. Wood-fired wild clay. 24 x 16 x 8. $900.
Will Dickert, Boat Form. Wood-fired stoneware. 6 x 8 x 22. $425.
Will Dickert, Linear Form. Wood-fired stoneware. 7 x 33 x 9. $975.
Michael Hunt & Naomi Dalglish, Fluted Oval Vase. Wood-fired local clay with Nuka glaze. 6.5 x 12 x 5. $175.
Michael Hunt & Naomi Dalglish, Onggi Shield Vase. Wood-fired local clay with slip and glaze. 19 x 14 x 5.5. $800.
Michael Hunt & Naomi Dalglish, Large Square Tray. Wood-fired local clay with wax resist and iron. 16 x 16 x 2. $475.
Michael Hunt & Naomi Dalglish, Carved Tray with Handles. Wood-fired local clay and Nuka glaze. 4.5 x 17.5 x 2. $125.
Michael Hunt & Naomi Dalglish, Square Bottle. Wood-fired local clay with slip glaze. 11 x 5 x 5. $175.
Michael Hunt & Naomi Dalglish, Long Tray No. 1. Wood-fired local clay with slip, sgraffito and green deco. 22 x 7.5 x 2. $375.
Sandy Lockwood, Black Jar. Wood-fired salt-glazed stoneware. 7 x 3 x 3. $450.
Sandy Lockwood, Orange Platter. Wood-fired and salt-glazed stoneware. 10 x 10. $900.
Sandy Lockwood, Cups. Wood-fired and salt-glazed stoneware. 5 x 3. $105 each.
William Baker, Triangle Vase. Stoneware, thrown and altered. 7 x 11 x 5. $220.
William Baker, Square Bowl. Stoneware, thrown and altered. 8 x 11 x 11. $495.
William Baker, Bottle No. 1. Stoneware, thrown and altered. 15 x 6 x 6. $325.
William Baker, Bowl No. 2. Stoneware, thrown and altered. 7 x 8 x 8. $260.
Josh Copus, Large Stone Vessel No. 8. Wood-fired wild clay. 24 x 8 x 7. $700.
Close up: Josh Copus, Large Stone Vessel No. 8. Wood-fired wild clay. 24 x 8 x 7. $700.
Eric Knoche, Untitled Form No. 3. Wood-fired stoneware with slips. 36 x 24 x 14. $5,700.
Close up of: Eric Knoche, Untitled Form No. 3. Wood-fired stoneware with slips. 36 x 24 x 14. $5,700.
David Peters, Bowl. Wood-fired local stoneware. 5 x 13.5 x 13.5. $375.
David Peters, Seven Sided Jar. Wood-fired local stoneware. 14.5 x 17.5 x 17.5. $1900.
David Peters, Four Sided Jar. Wood-fired local stoneware. 8 x 13 x 13. $600.
Eric Knoche, Untitled Form No. 2. Wood-fired stoneware with slips. 18 x 16 x 14. $2,800.
Eric Knoche, Untitled Form No. 1. Wood-fired stoneware with slips. 16 x 18 x 15. $3,000.
Akira Satake, Sculpture No. 1. Wood-fired porcelaneous clay. 12.5 x 7.5 x 5. $1,800.
Akira Satake, Sculpture No. 5. Wood-fired porcelaneous clay. 6.25 x 8 x 7. $725.
Great Pots from the Traditions of North & South Carolina: Exhibition at the Pottery Center in Seagrove, North Carolina.
Over the past year, Mark has been busier than usual. As well as making his usual quota of pots, he's been helping to organise the International Woodfire Conference (which happened a few weeks ago) and the Great Pots exhibition that coincided with it. During the winter, after we 'd fired the salt kiln, Mark drove around the South meeting collectors and pickers and dealers, trying to find the very best examples of traditional North and South Carolinian pottery. The idea was to showcase the rich history of pot making in this area to all of the world-class woodfire potters who would be visiting for the conference.
The proceedings opened at the Pottery Center, with the Great Pots on display. We ate NC barbeque, (pulled pork, collards, hush puppies, and the like), chatted with new and old friends and took in the pots, excited for the weekend's events to come.
This exhibition and accompanying book (above; it can be purchased here) acts as a sequel to Mark's previous exhibition and book, The Potter's Eye. A few of the same pots were included, such the one from the cover of The Potter's Eye by Solomon Loy. It was a real treat to see this one up close! When I asked why he wanted a few of these previous pots, he simply said, "I just had to show those ones"... they acted as a starting point -- a measure of quality. The choice of pots was mostly a matter of which ones Mark particularly liked and felt needed to be shown.
This makes the exhibition all the interesting because his perspective is different from the usual art curator or collector. Being a potter, he appreciates all aspects of the pots, from the forms, to the decorations, to the way the handles were put on, to the firing, to the clay etc etc. In this way, the exhibition and accompanying book are truly a sequel to The Potter's Eye.
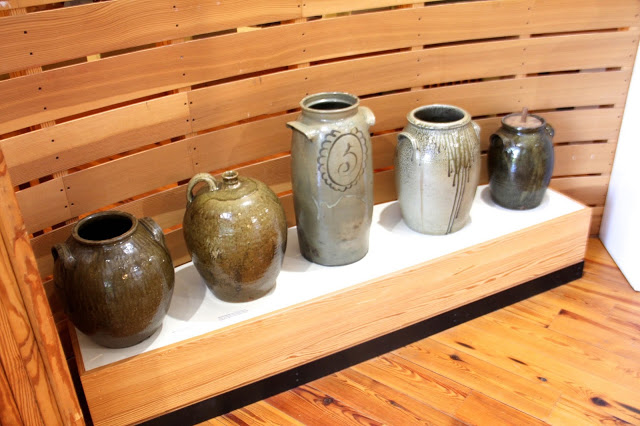
There are over 150 pots in the exhibition and book, each with a little lyrical note from Mark portending to why he included that particular pot. The pots are organised into five sections, with informative, engaging essays from authorities on them: Linda Carnes-McNaughton on earthenware and the pots from Alamance County, NC, Charles (Terry) Zug on alkaline and salt-glazed wares, Philip Wingard on South Carolina stoneware. As there were so many pots to fit into the Pottery center, Mark was creative in his display; arranging groups of pots together, almost in still life scenes. This was partly out of necessity but also inspired by an exhibition of ceramics called "Parades," organised by Gwyn Hanssen Pigott (2006-2008), at the Freer Gallery of Art in Washington DC.
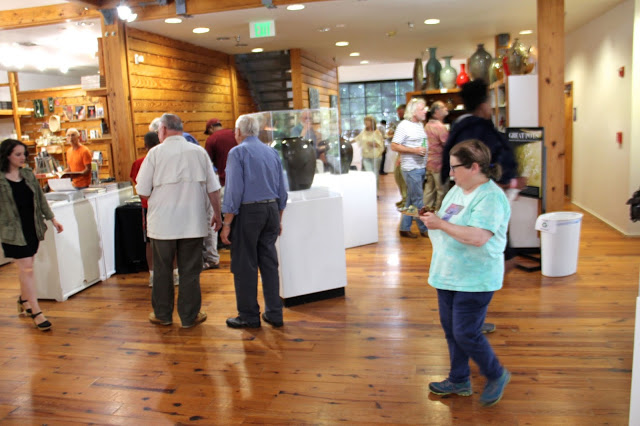
I went back and revisited the exhibition last weekend with less people around and was amazed by the quality and breadth of the work. It was wonderful to be able to walk around them slowly, feeling the surfaces and examining the clay bodies. The pots have a power in person; particularly the larger jars, churns, and jugs. I love the wide bellies, high shoulders, and strong forms of many of these pots. The wide range of wood-fired surfaces struck me too; all different permutations of wood ash deposits, salt and alkaline glazes, over and under fired, as well as dainty pinkish deer spots. I particularly enjoyed the accidental surfaces from firings gone awry; you can see some pots where the kiln bricks melted glassy drips onto them. But also, in contrast to these gnarlier examples, I loved seeing the crisp, delightful incising of Chester Webster's work.
To start this post, I have included a few pictures of the exhibition as it was laid out in the Pottery Center. These quick snaps don't really do the pots justice, but give a sense of the exhibition. Below those are some of the pictures used in the book (which Mark kindly sent me), taken by professional craft photographer Jason Dowdle.
The exhibition is up until July 22nd, 2017, so get over to Seagrove and check it out if you can! If not, there's always the book. It is a very nicely put-together tome with excellent photographs, as you should get a taste of in this post.
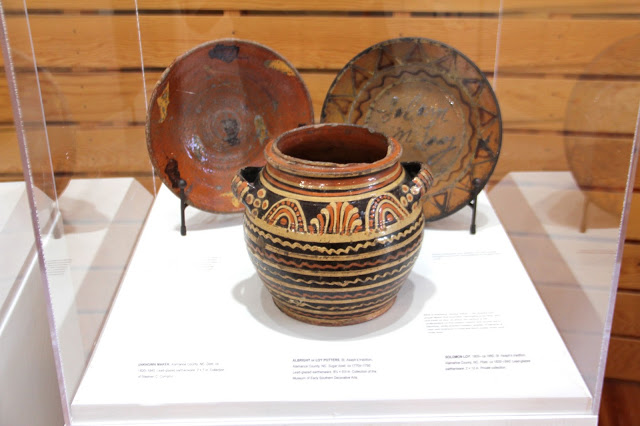
Now on to Jason Dowdle's professional pictures. I've included the entries as they are in the book: with all the details of the pots and Mark's comments underneath. Enjoy!
Alkaline Glazed Stoneware (NC)
Alamance County (NC) Salt Glaze
Earthenware from North Carolina
The proceedings opened at the Pottery Center, with the Great Pots on display. We ate NC barbeque, (pulled pork, collards, hush puppies, and the like), chatted with new and old friends and took in the pots, excited for the weekend's events to come.
This exhibition and accompanying book (above; it can be purchased here) acts as a sequel to Mark's previous exhibition and book, The Potter's Eye. A few of the same pots were included, such the one from the cover of The Potter's Eye by Solomon Loy. It was a real treat to see this one up close! When I asked why he wanted a few of these previous pots, he simply said, "I just had to show those ones"... they acted as a starting point -- a measure of quality. The choice of pots was mostly a matter of which ones Mark particularly liked and felt needed to be shown.
This makes the exhibition all the interesting because his perspective is different from the usual art curator or collector. Being a potter, he appreciates all aspects of the pots, from the forms, to the decorations, to the way the handles were put on, to the firing, to the clay etc etc. In this way, the exhibition and accompanying book are truly a sequel to The Potter's Eye.
There are over 150 pots in the exhibition and book, each with a little lyrical note from Mark portending to why he included that particular pot. The pots are organised into five sections, with informative, engaging essays from authorities on them: Linda Carnes-McNaughton on earthenware and the pots from Alamance County, NC, Charles (Terry) Zug on alkaline and salt-glazed wares, Philip Wingard on South Carolina stoneware. As there were so many pots to fit into the Pottery center, Mark was creative in his display; arranging groups of pots together, almost in still life scenes. This was partly out of necessity but also inspired by an exhibition of ceramics called "Parades," organised by Gwyn Hanssen Pigott (2006-2008), at the Freer Gallery of Art in Washington DC.
I went back and revisited the exhibition last weekend with less people around and was amazed by the quality and breadth of the work. It was wonderful to be able to walk around them slowly, feeling the surfaces and examining the clay bodies. The pots have a power in person; particularly the larger jars, churns, and jugs. I love the wide bellies, high shoulders, and strong forms of many of these pots. The wide range of wood-fired surfaces struck me too; all different permutations of wood ash deposits, salt and alkaline glazes, over and under fired, as well as dainty pinkish deer spots. I particularly enjoyed the accidental surfaces from firings gone awry; you can see some pots where the kiln bricks melted glassy drips onto them. But also, in contrast to these gnarlier examples, I loved seeing the crisp, delightful incising of Chester Webster's work.
To start this post, I have included a few pictures of the exhibition as it was laid out in the Pottery Center. These quick snaps don't really do the pots justice, but give a sense of the exhibition. Below those are some of the pictures used in the book (which Mark kindly sent me), taken by professional craft photographer Jason Dowdle.
The exhibition is up until July 22nd, 2017, so get over to Seagrove and check it out if you can! If not, there's always the book. It is a very nicely put-together tome with excellent photographs, as you should get a taste of in this post.
I love these earthenware pots, particularly the sugar bowl up front. It is so alive and expressive, over the top in its slip-trailed decoration but humble in form.
This large mixing bowl is amazing. The glaze must have been applied really thickly as it ran down and puddled in one side of the base.
This pot is attributed to Milton Rhodes (1843-52). I find the decoration very odd. You can see it two ways; either a slip trailed woman in a hooped skirt is at the center, with flowers up above, or the flowers are eyes, her torso is a nose and her skirt is a gaping mouth. Great shape, but I find the decoration rather unsettling!
Mr. Hewitt giving a talk about how the exhibition came to fruition, in the teaching wing of the Pottery Center. |
One gallon crock stamped JD CRAVEN BROWER'S MILL, N.C. I rather fancy this one as a bread bin.
Jugs!
I like how slender this whisky jug is. Pretty light too (not that I picked it up or anything).
I really like this Chester Webster jug too: despite being underfired, it has a lot going on in the surface. I like shape of the the neck and lip too.
Alkaline Glazed Stoneware (NC)
DANIEL SEAGLE, ca 1805–1867, Lincoln County, NC. Fifteen-gallon jar. Alkaline-glazed stoneware. 18 × 19 in. Collection of Quincy, Betty & Samuel Scarborough.
Orthodox, generous, and calm, with somber notes, Daniel Seagle’s giant pot possesses an accuracy and girth that set a standard.
DANIEL SEAGLE, ca 1805–1867, Lincoln County, NC. Five-gallon jar. Alkaline-glazed stoneware. 16 × 13 in. Collection of Danny Richard.
Pottery collector Danny Richard got a call from someone in Lincoln County saying they’d found old pots buried under their house. They knew he was interested. Covered in dirt, a pig in a poke, he paid the price. All except one looked cracked or broken. He put them in his pickup, drove away, then stopped by a creek, took them to the water, and used his shirt to wash away the dirt. This one was baptized intact.
JAMES FRANKLIN SEAGLE, 1829–1892, Lincoln County, NC. Half-gallon jug. Alkaline-glazed stoneware. 9½ × 6 in. Collection of Scott & Wendy Smith.
Another talented Seagle, Daniel’s son James Franklin, precise, disciplined, carrying on where his father left off. Different times though, the pre– and post–Civil War South.
ISAAC LEFEVERS, 1831–1864, Lincoln County, NC. Five-gallon jug. Alkaline-glazed stoneware. 18 × 13 in. Collection of Quincy, Betty & Samuel Scarborough.
IL: tragically rare letters. The orphaned apprentice who died at thirty-three. The stick figure–like drips, from excess glaze tipped back after the pot was dunked, are deliberate. If you pay attention, control of process generates ornament.
SYLVANUS HARTSOE, 1850–1926, Lincoln County, NC. Large rundlet with glass melt. Alkaline-glazed stoneware. 13 × 18 in. Collection of Allan & Barry Huffman.
A submarine or a “medicine” bottle? Glaze application drips and a pool of glass give a liquid air to this curious container.
UNKNOWN MAKER, Lincoln County, NC. Five-gallon jar with glass runs, ca 1875. Alkaline-glazed stoneware. 16¼ × 13 in. Collection of Scott & Wendy Smith.
Moore and Randolph County (NC) Salt Glaze
CHESTER WEBSTER, 1801–1882, Fayetteville, NC. One-gallon jug, underfired with pale wad marks. Salt-glazed stoneware. 6 × 10 in. Collection of Quincy, Betty & Samuel Scarborough.
Discarded, damaged, and unearthed at the shard heap, it is an exquisite reject. The frost nipped it, it never grew up, it fell before its time. Contemporary in its ethereal wad markings, it held promise, but never water.
CHESTER WEBSTER, 1799-1882, Randolph County, NC. Three-gallon jar with incised bird, fish, and date, 1851. Salt-glazed stoneware. 15 × 12 in. Collection of Tommy & Ann Cranford.
A whimsical bird plucks a fly from the date-filled air, while a fish pirouettes behind. Chester’s humor didn’t fester.
CHESTER WEBSTER, 1799–1882, Randolph County, NC. Two-gallon jug, with incised bird. Salt-glazed stoneware. 15 × 9 in. Collection of Quincy, Betty & Samuel Scarborough.
A perfectly poised profile rewarded with a trilling bird, or is it catching flies? Either way it’s smiling.
CHESTER WEBSTER, 1799–1882, Randolph County, NC. Four-gallon jug, with incised heron. 18 × 10 in. Collection of Tommy & Ann Cranford.
Webster incised herons, Cardew painted them. One flew overhead when I first stood where my chimney would be.
T. W. CRAVEN, 1829–1858, Randolph County, NC. Ten-gallon double-handled jug, with cobalt sumac tree. Salt-glazed stoneware. 21 × 14 in. Collection of Quincy, Betty & Samuel Scarborough.
Bewitched, bothered, and bewildered, this captivating beauty was damaged, perhaps by frost, and crudely repaired with epoxy. There’s no hiding loveliness, though.
NICHOLAS FOX, 1797–1858, Chatham County, NC. Half-gallon jug, with kiln drips. Salt-glazed stoneware. 7 × 6 in. Collection of William Ivey.
A sweet shape with juicy drips and luscious ash.
J. J. OWEN, 1830–1905, Moore County, NC. Two-gallon patent jar. Salt-glazed stoneware. 17 × 10 in. Collection of Jugtown Pottery.
Beaten, broken, maybe even shot, this jar is an invalid. Dignified nonetheless by its spectacular tonal variation, its hole is a badge of honor for years of service.
J. H. OWEN, 1866–1923, Moore County, NC. Drain tile. Salt-glazed stoneware. 15 × 7 in. Collection of Jugtown Pottery.
A piece of minimalist abstract art? It depends on the context.
TEAGUE FAMILY, Randolph County, NC. Grave Marker for James R. Teague, 1938. Salt-glazed stoneware. Gift of Charles G. Zug III, Ackland Art Museum, University of North Carolina at Chapel Hill. 84.42.1. (Photographs by Scott Richard Hankins).
This one gives me the shivers.
Alamance County (NC) Salt Glaze
SOLOMON LOY, 1805–ca 1860, Alamance County, NC. One-and-a-half-gallon pitcher with ash runs and kiln drips. Salt-glazed stoneware. 11½ × 9 in. Collection of Robert & Jimmi Hodgin.
Its shape is stiff and squat, but its delicately pinched throat and spout combine with the glistening ash runs and a diaphanous kiln drip to make it spectacular.
SOLOMON LOY, 1805–ca 1860, Alamance County, NC. One-gallon jug with ash runs and kiln drips. Salt-glazed stoneware. 11 × 7 in. Collection of Robert & Jimmi Hodgin.
Add more colors to the mix, and here’s another wonder. Dark patches from salt shadows and a swath of slow-cooled ash distinguish this treasure.
GROUP OF CANNING JARS
Sleek, narrow-mouthed, and infinitely varied, these stunning canning jars are unique to Alamance County. Like leaves they shimmer and glow, all dappled and drippy, set up for a show.
TIMOTHY BOGGS, 1849–ca 1910, Alamance County, NC. Canning jar. Salt-glazed stoneware. 11 × 7½ in. Collection of Robert & Jimmi Hodgin.
Humpty Dumpty had a great fall, but didn’t quite break. Injured but not discarded, no longer useful but valuable nonetheless. An exotic, wild, damaged beauty, treasured despite its flaws, for its flaws.
SOLOMON LOY, 1805–ca 1860, Alamance County, NC. Eight-gallon jar. Salt-glazed stoneware. 20 × 12 in. Collection of Joseph & Amanda Sand.
Of all the potters in the South, Solomon Loy seems to have deliberately composed the abstract appearance of his stoneware pots, artfully finessing the process of salt firing, with its accompanying kiln drips and ash runs, and consciously layering seductive colors and enigmatic textures.
SOLOMON LOY, 1805–ca 1860, Alamance County, NC. Ten-gallon jar with ash runs and kiln drips, stamped “S. LOY 1856 10.” Salt-glazed stoneware. 19 × 14 in. Collection of Robert & Jimmi Hodgin.
An amputee, with stumps where its handles used to be, this big jar remains magnificent, proud, and undaunted.
Earthenware from North Carolina
JACOB WEAVER II, 1774–1846, Catawba County, NC. Plate, ca 1790. Lead-glazed earthenware. 4 × 9 1/2 in. Collection of Tommy & Ann Cranford.
Unlike most of the early earthenware potters in North Carolina, who worked in the eastern Piedmont, Jacob Weaver built his kiln in Catawba County, known primarily for its later alkaline-glaze tradition. This kiln site and plate were only recently discovered. Simple, controlled, and lively, the plate has a beautifully executed set of polychrome slip-trailed lines with sgraffitoed rim decoration. Incredibly, it has remained in perfect condition since the 1790s.
SOLOMON LOY, 1805– ca 1860, St. Asaph’s tradition, Alamance County, NC. Small plate, ca 1820–1840. Lead-glazed earthenware. 2 × 6½ in. Collection of Robert & Jimmi Hodgin.
Fleshy pink blotches with black and white dots. A straightforward description says little about the wonders of this masterpiece. Warm and embraceable, with a cloudy gray quadrant where the smoke choked the gritty clay into soft, blushing halos. Dots float along the surface like confetti.
Attributed to WILLIAM DENNIS New Salem Quakers, Randolph County, NC. Plate, ca 1800. Lead-glazed earthenware. 2¼ × 10¾ in. Collection of Stephen C. Compton.
An autumnal mood resides in the fernlike decoration and deciduously swaging border of this plate. Its character marks the reliability of the cyclical rhythm of the seasons.
SOLOMON LOY, 1805–ca 1860, St. Asaph’s tradition, Alamance County, NC. Miniature mug, ca 1820–1840. Lead-glazed earthenware. 2½ × 3½ in. Collection of Tommy & Ann Cranford.
One can only imagine the delight a youngster would have using this sweet spattered mug, or entertaining with it as part of a doll’s tea set. Childs play, imaginative and unbroken.
Pots from South Carolina
THOMAS CHANDLER, 1810–1854, Thomas Chandler Stoneware Factory, Kirksey’s Crossroads, Edgefield District, SC.Double-handled five-gallon jug with slip-trailed floral motif, stamped “CHANDLER MAKER,” ca 1850. Alkaline-glazed stoneware. 19 × 11 in. Collection of David Ward.
Soft color on strong form while the decoration sits perfectly on the shoulder. Big blue celadon, calm and authoritative.
THOMAS CHANDLER, 1810–1854, C. Rhodes Factory, Shaw’s Creek, Edgefield District, SC. Three-gallon jar with slip-trailed floral motif, ca 1850. Alkaline-glazed stoneware. 15 × 11 in. Collection of Jim Witkowski.
The shape is superb, the handles snug, and flowers flow — alive, deftly drawn. A different performance on each side, all bathed in luxuriant celadon, the perfect tone. Layer upon layer of slightly changing excellence, Chandler’s repeated themes and variations resemble a fugue.
UNKNOWN MAKER, C. Rhodes Factory, Shaw’s Creek, Edgefield District, SC. Five-gallon Jar, slip-decorated with a “number flower” on one side and a flower on the other, ca 1850. Alkaline-glazed stoneware (with repaired neck). 14½ × 12 in. Collection of John LaFoy.
Does a repair ruin a pot? Is such a flaw acceptable in an exhibition? The rest of the pot is fabulous, the “5” flower (the rare Rhodesian genus flora numerica), with a second exotic on its rear. But that green neck? Probably done with great care in the 1960s by someone who should have known better, it’s like a blemish on a pretty forehead.
UNKNOWN MAKER, C. Rhodes Factory, Shaw’s Creek, Edgefield District, SC. Three-gallon jar, slip-decorated with the profile of a man on one side and a flower on the other, ca 1840. Alkaline-glazed stoneware. 14½ × 12 in. Collection of John LaFoy.
The slip was dark, the figure’s race unclear. A person in profile with hair, an eye, an ear, teeth, a kerchief, buttons, frills, and fingers, warm ochre red bleeding through the glaze. A complex moment recorded. A life.
UNKNOWN MAKER, Upstate South Carolina, or Thomas Chandler School, Martintown Road Pottery, Kirksey’s Crossroads, Edgefield District, SC, or John D. Leopard, Bacon Level, Randolph County, Alabama. Ten-gallon double-handled jug, with red ochre bleeds and residual ochre nuggets. Alkaline-glazed stoneware. 20 × 14 in. Collection of David Ward.
UNKNOWN MAKER, Upstate South Carolina, or Thomas Chandler School, Martintown Road Pottery, Kirksey’s Crossroads, Edgefield District, SC, or John D. Leopard, Bacon Level, Randolph County, Alabama. Ten-gallon double-handled jug, with red ochre bleeds and residual ochre nuggets. Alkaline-glazed stoneware. 20 × 14 in. Collection of David Ward.
LINNAEUS LANDRUM, ca 1829–1891, Landrum Pottery, Eight Mile Branch, Columbia, SC. Three-gallon jar with feldspar glaze, stamped twice “L.M. Landrum, Columbia S.C.,” ca 1860. Alkaline-glazed stoneware. 15½ × 11½ in. Study collection of Philip & Deborah Wingard.
Maybe it’s the crazing, the color, the shape, or the feeling it conveys? Somehow the gray-green, silky soft patina and sweet shape make this one an absolute winner.
DAVID DRAKE, ca 1800–1870, Lewis Miles Pottery, Horse Creek, Edgefield, SC. Twenty-gallon jar inscribed, “Nineteen days before Chrismas Eve — Lots of people after its over, how they will greave . . . LM, Dave, Dec 6 1858.” Alkaline-glazed stoneware. 21 × 19½ in. Collection of Corbett Neal Toussaint.
Dave Drake’s verse haunts, as do others on his pots. Some of them express resistance in the slave South. This one, for instance, may refer to the grim practice of giving slaves to a new owner as a Christmas present, or of leasing enslaved laborers to other area slaveholders for one-year stints, starting on New Year’s Day. Good tidings on Christ’s birthday? Joy, peace, love… and families torn apart? The enslaved potter Dave Drake exposes their grief and suffering through his hands, intellect, and voice. Drake was taught to read and write---a star that was allowed to shine, while others were not.
Let there be light!
Kiln Opening at Mark Hewitt's Pottery, Firing Elle, Spring 2017.
The pottery looked as clean and ship-shape as I have ever seen it by the time people arrived on Saturday morning. It was a lovely day and a good crowd showed up early; there was a line by the time I arrived.
The firing went well -- we've been continuing to experiment with glazes, in particular the celadons based on this Salisbury pink granite which Mark collected from a local quarry. We've been focusing on trying to make it craze less as a bisque glaze (with high percentage of the granite) and developing raw glazes with it that still look attractive. Still some refining to do but we're definitely getting closer, and we're pleased with how many of the pots came out. I plan to do a post with our findings and test results in more detail some time this spring.
There are still plenty of pots left for next weekend; we saved some to put out fresh.
Saturday April 29, 9 - 5pm, and Sunday April 30, 12pm - 5pm.
Mark addressing the congregation early Saturday morning. |
People flow down to the barn. |
We lined Mark's big pots up this time, rather than having them in the round. I think they look great down in the field like this.
Big pots. Monumental pecan tree in the background. |
Mark Hewitt, Big Pots. Spring 2017. |
Mark Hewitt, Bloom. Large stoneware vase. $4,500. |
Mark Hewitt, Tears for America. Large ash glazed stoneware jar. Spring, 2017. $12,000. |
Close up of Tears for America. |
Mark Hewitt, Pirouette. Large celadon stoneware vase. Spring, 2017. $9,500. |
Mark Hewitt, The Raver. Large ash glaze stoneware vase. Spring, 2017. $9,500. |
One lady getting up close and personal with The Raver. |
Close up of Raver. |
Mark Hewitt, Wiggle Waggle. Large celadon stoneware vase. Spring, 2017. $6,500. |
Close up of Wiggle Waggle. |
Mark Hewitt, Into the Night. Large tenmoku stoneware vase. Spring, 2017. $6,500. |
Close up of the glass drips on Into the Night. |
Mark Hewitt, Black Eye. Large salt-fired stoneware vase. $5,000. |
Close up of Black Eye. |
Into the barn...
The roses are out in force. |
Mark Hewitt, Platter and ice cream bowls. Spring, 2017. |
Mark Hewitt, Pitcher and barrel mug. Spring, 2017. |
Mark Hewitt, Ginger Jar. Spring, 2017. |
Mark Hewitt, Vases. Spring, 2017. |
Mark Hewitt, Gravemarkers. Spring, 2017. |
Mark Hewitt, Two Part Vase. Spring, 2017. |
Mark's little blurb for this last cycle. |
Mark Hewitt, Two Part Vase. Spring, 2017. |
Mark Hewitt, Iced Tea Tumblers. Spring 2017. |
Mark Hewitt, Ginger Jar. Spring, 2017. |
Mark Hewitt, Ginger Jar. Spring, 2017. |
A couple happy with the ginger jar they had picked up. |
Mark Hewitt, Ginger Jar. Spring, 2017 |
Mark Hewitt, Umbrella Pot and Mug. Spring, 2017. |
Mark Hewitt, Various Pots, Spring 2017. |
Mark Hewitt, 10 Gallon Pots (and a few mugs). Spring, 2017. |
Will they all fit? |
Here's a couple of pics a mix of Stilly and I's pots on the shelves, just before the customers got into them:
Blue celadons on the top, green celadons in the middle, and tenmoku on the bottom shelf. |
Now a smattering of Stillman's pots...
Stillman Browning-Howe, Various Pot. Spring, 2017. |
Stillman Browning-Howe, Tankards. Spring, 2017. |
Stilly's blurb. |
Stillman Browning-Howe, Bud Vases. Spring, 2017. |
A couple checking out one of Stillman's jars. |
Lastly, some of mine...
Hamish Jackson, Various Pots. Spring, 2017. |
Hamish Jackson, Wall Vases. Spring, 2017. |
Hamish Jackson, Wall Vases. Spring, 2017. |
Hamish Jackson, Souffle Dish. Spring, 2017. |
Hamish Jackson, Teapot. Spring, 2017. |
Hamish Jackson, Canister Jar. Spring, 2017. |
Hamish Jackson, Two Part Vase. Spring, 2017. |
Hamish Jackson, Canister Jar and Cruets. Spring, 2017. |
Hamish Jackson, Small and Large Cruets. Spring, 2017. |
I took some of my favorites at home with a Flotone backdrop:
Hamish Jackson, Celadon Bud Vase. Spring, 2017. Sgraffito under blue celadon glaze. |
Hamish Jackson, Small Footed Bowl. Spring, 2017. Red slip with white and red slip dots applied when wet and moved around to create this marbled effect. |
Hamish Jackson, Barrel Mug. Spring, 2017. White slip dots under green celadon glaze. |
Hamish Jackson, Tea Tumblers. Spring, 2017. Red and white slip trailing under blue celadon glaze. |
Hamish Jackson, Creamer. Spring, 2017. White slip circles and red slip dots. I love how clean and translucent this glaze came out. |
Hamish Jackson, Souffle Dish. Spring, 2017. From the front stack of the kiln: it got a lot of ash hitting the surface. |
Hamish Jackson, Large tenmoku teapot. Spring, 2017. Red and white slip under tenmoku. |
Hamish Jackson, Family sized celadon teapot. Spring, 2017. Brushed red slip and white slip dots under green celadon glaze. |
Hamish Jackson, Family sized tenmoku teapot. Spring, 2017. This was fired on the floor of chamber two, at the foot of the big pots. |
Hamish Jackson, Yunomi. Spring, 2017. Shino with red iron oxide over the top, wood ash collected on rim. |
Hamish Jackson, Pair of celadon cruets. Spring, 2017.Sgraffito under two different celadons. |
Hamish Jackson, Celadon cider jar. Spring, 2017.White and red slip trailing under green celadon glaze. |
Hamish Jackson, Shino cider jar. Spring, 2017.Fired in the front stack but protected by a bag wall; the surface up close is luminescent and sparkles green and blue. |
Hamish Jackson, Quart pitcher. Spring, 2017.Blue glass under celadon with bone ash addition. We only got these red drips on a few pots -- not really sure why. |
Hamish Jackson, Shino soy dishes. Spring, 2017.Red iron oxide under shino. |
Hamish Jackson, Canister Jar. Spring, 2017.Brushed shino glaze and wood ash (this one was buried in wood ash next to a stoke hole). |
Hamish Jackson, Canister Jar. Spring, 2017.Red and white slip trailing under green celadon glaze. |
Hamish Jackson, Canister Jar. Spring, 2017.Red and white slip trailing under tenmoku glaze. |
Hamish Jackson, Yunomi. Spring, 2017. Red iron oxide under green celadon glaze: front stack. I don't know why but this glaze has such a silky soft feel to it. |